Technology
Additive Friction Stir Deposition (AFSD) is a low temperature process which may be used to build, coat, join or repair three-dimensional, large metal components. AFSD is a versatile metal additive manufacturing process as there are virtually no size, alloy or feedstock limitations. The technology has its roots in Friction Stir Welding which has been studied for almost 30 years.
Current Materials
Almost any metal alloy available in the industrial market, both ferrous and non-ferrous alloys.
FAQ
- Uses square or round bar in many alloys readily available at competitive cost.
- High deposition rates.
- No chambers or powder beds needed.
- No need for de-binding, sintering or HIPing.
- Able to print fully dense parts with a wrought microstructure.
- Mechanical properties meet or exceed properties of either traditionally manufactured or other additively manufactured components.
- Three-dimensional large-sized components may be built.
- Solid-state process which greatly reduces residual stress.
Rate is alloy-dependent but measured in kilograms per hour. For some alloys it can be almost 10 kg/hr.
No, it only uses contact friction heat to achieve metal bonding.
No, AFSD is done in open air environment. If a particular alloy application requires an inert atmosphere, local shielding is possible.
Basically no, since the process is not done inside a chamber neither does it use powder beds.
Excellent. AFSD is a thermo-mechanical process which achieves a fine-grained wrought microstructure through “stirring”. This means mechanical properties are usually better than those obtained through other manufacturing processes.
You can go down to about 12mm (1/2").
Yes. Coating thickness can be measured in microns (or thousandths of an inch).
Featured Applications
Apply metal layers to existing components or raw material to expand inventory use through coating, added features, increased environmental resistance or repair damaged parts.
Repair
Cast, wrought or forged components of almost any metal alloy.
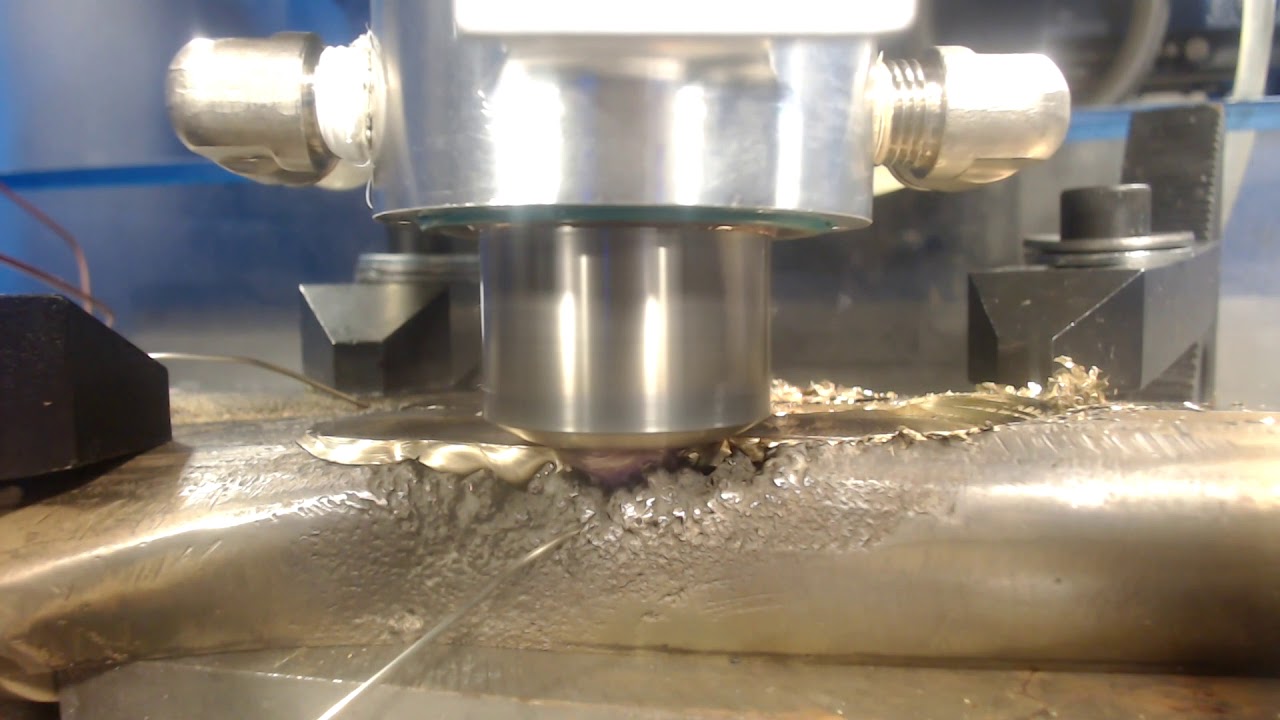
Coat
Obtain a metallurgical bond between the coating layer and substrate part.
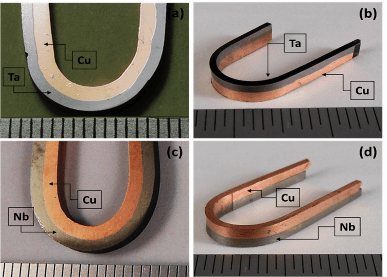
Add features
To improve part performance or add complexity to specific locations.
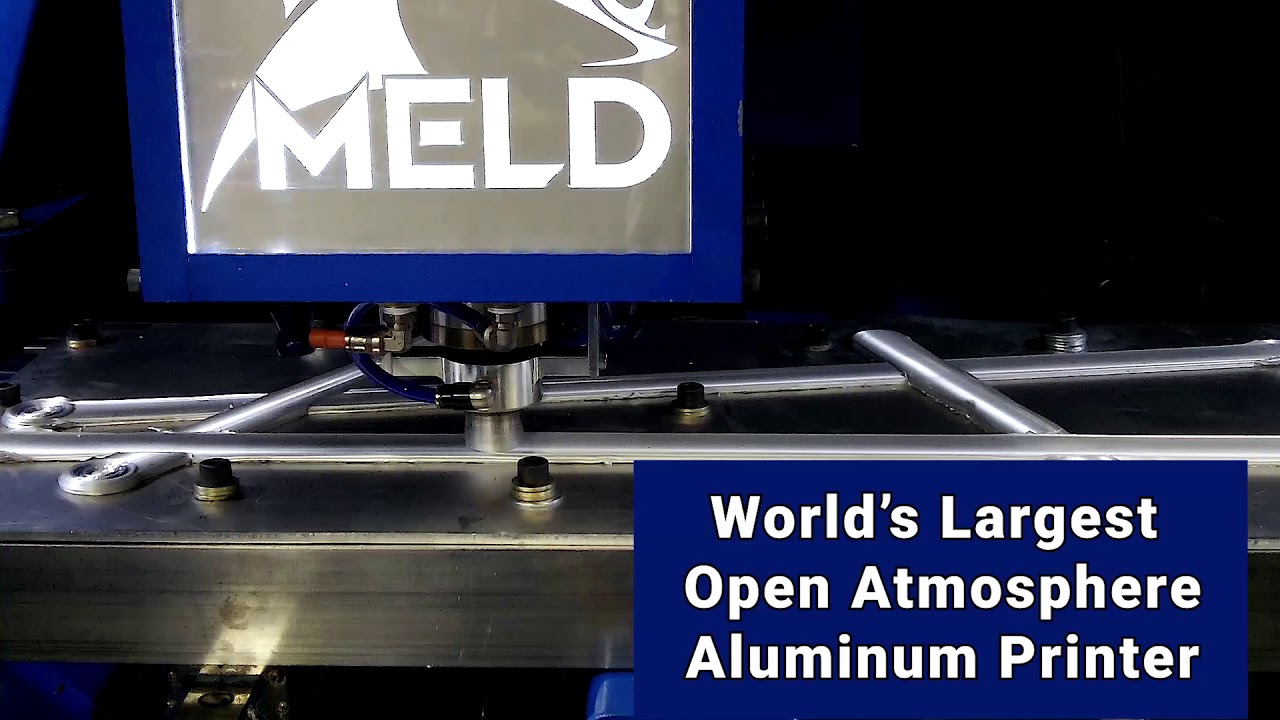
Join
Dissimilar metals without dealing with the problems associated with melting processes.
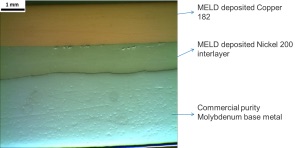
Research & Development
AFSD is an active field of research around the world using MELD® Manufacturing technology:
- Deakin University in Australia
- The Advanced Materials and Manufacturing Processes Institute at the University of North Texas in USA
- Showcased at the United States Air Force AFWERX FUSION Virtual event